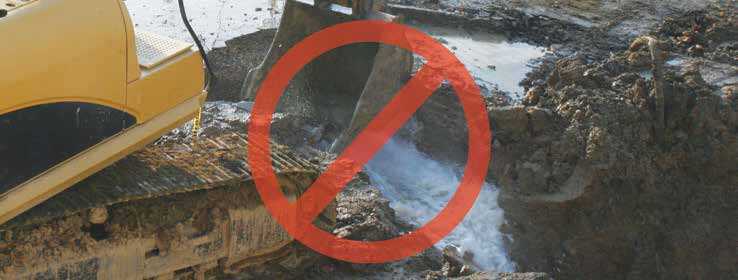
This article was published in the 2025 Excavation Safety Guide.
Preventing utility damage can be challenging, especially if you don’t have a comprehensive file showing what you are doing. In today’s utility damage prevention landscape, capturing and documenting best practices is crucial for all stakeholders. Here’s a detailed guide to ensure you have all the necessary documentation to prevent damage and associated claims effectively.
1. Verify Positive Response Documentation
Review each positive response to ensure all facilities are marked or confirmed as no conflict.
Many individuals working in the field lack an understanding of what constitutes a “positive response” and its significance for safe digging. Ensure you not only receive a “paper ticket” but also verify the positive response documentation on-site. Many field teams neglect to check if all facilities are marked or if additional actions are required, leading to potential issues if damage occurs. In some regions, such as Florida, only a few positive response codes confirm facilities are marked. The majority indicate that further action is needed.
2. Photograph Locate Marks
Photograph all locate marks to confirm they match those listed in the positive response.
Photographing locate marks is a simple yet powerful practice that can aid in preventing damage. One major provider of directional drilling services required subcontractors to take photos of locate marks, significantly reducing damage incidents. Use tools to document the placement and distance of locate marks relative to the location of buried facilities. Including a 12-foot range pole or level rod in photos provides a perfect perspective for usable documentation. This practice helps in recreating the scene if marks are destroyed during construction.
3. Pothole for Accuracy
Pothole facilities near work areas to verify the accuracy of the marks and document measurements with photos.
Potholing is crucial for confirming the accuracy of utility marks. Document, with photos, the depth and distance from the locate marks to buried facilities using tools like range poles and rulers. This verification process helps in preventing damage and provides valuable evidence if a claim arises. Share this documentation with utility companies to improve overall locate accuracy.
4. Document Utility Markers
Photograph all utility marker pylons in or near the work site.
Large gas line markers, fiber optic pylons, etc. should be photographed to ensure all lines are properly marked. This documentation helps identify potential issues with unmarked facilities that could lead to traumatic injuries as well as costly damage if not addressed.
5. Report Unmarked Surface Indications
Photograph and report surface indications of unmarked facilities to 811.
Surface indications, such as pedestals or other markers, should be documented and reported if they are not marked. This practice helps in identifying potential oversight by locators and ensures all possible indicators of facilities are addressed before excavation begins.
6. Use Technology for Documentation
Effective communication and documentation practices are essential for damage prevention.
Consider using cloud-based technology platforms that integrate with both desktop and mobile devices. The software allows field crews to document their activities, take and upload photos, and ensure best practices are followed. Senior management can monitor compliance in real-time, providing a comprehensive view of the damage prevention efforts across the organization.
By implementing these steps, you can significantly enhance your ability to prevent damage and defend against claims effectively. Proper documentation reinforces your commitment to best practices in utility damage prevention and supports your defense in case of damage.