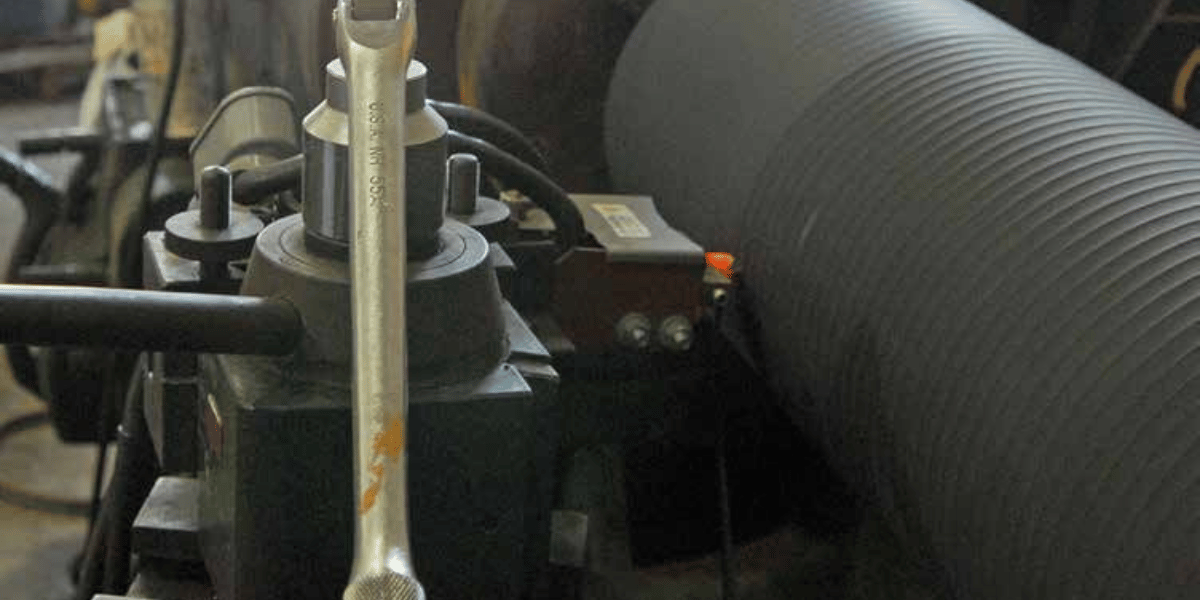
Did you know that offshore structure failure due to pipeline corrosion costs up to $1.372 BILLION per year? It’s no secret that external corrosion can result in major disaster. If not detected within a certain amount of time, the pipeline can burst into flames, resulting in hundreds of thousands of dollars in damage costs and fines, and sometimes even death. As the industry progresses and we begin drilling farther into the gulf, the need for protective pipeline coating is at an all-time high.
Thankfully, this is where rubber comes in. With a rubber coating and proper pipeline maintenance, we can ensure that pipelines and their surrounding environments are protected. In most cases, rubber-based coatings are used to line, case, and protect equipment and structures inside of the splash zone from external corrosion. The reason this type of coating is growing in popularity is because it is much less rigid than most other materials, and it’s also incredibly strong, versatile, and durable.
Given its special qualities, this material is able to take on more stress and is harder to break down than other materials. Rubber can protect against nearly all causes of corrosion, including the ozone, abrasive seawater and the damaging effects of sea life, ultraviolet rays, salinity, oxygen, and the collision of boats and other floating debris.
Benefits of Rubber Elastomer Coating
Simply adding a rubber coating to subsea pipelines can protect against all of the aforementioned hazards and more. The unique characteristics of rubber coatings help to extend the lifespan of pipelines, making them resistant to virtually anything that Mother Nature throws at it. J-tubes, rise clamps, platform legs and diagonals, spools, and risers can also be coated with rubber for protection.
Making pipelines safer with rubber saves both time and money in several different areas. You no longer have to worry about damage and replacement costs or repair fees. Also, the use of rubber aids in decreasing the need for untimely setbacks due to unplanned maintenance, complying with health, environmental, and safety policies, as well as boosting plant availability. Specific rubber coatings can be made to permanently bond to any metal surface, will not crack or dis-bond, and will not require regular maintenance.
When it comes to pipeline protection, rubber is priceless. Resistant to weathering, elements, and most oils, rubber coating is your best bet when it comes to damage protection. Certain forms can also act as a non-conducive thermal insulation and stop biofouling from occurring. Using materials other than rubber to coat pipelines creates a risk of leaking and breakage in coating, which is just as dangerous as having no coating at all and can cost you production time and revenue.
Because nature cannot be tamed, the best chance at corrosion prevention and pipeline protection is to invest in a rubber coating for your structures.
Comments