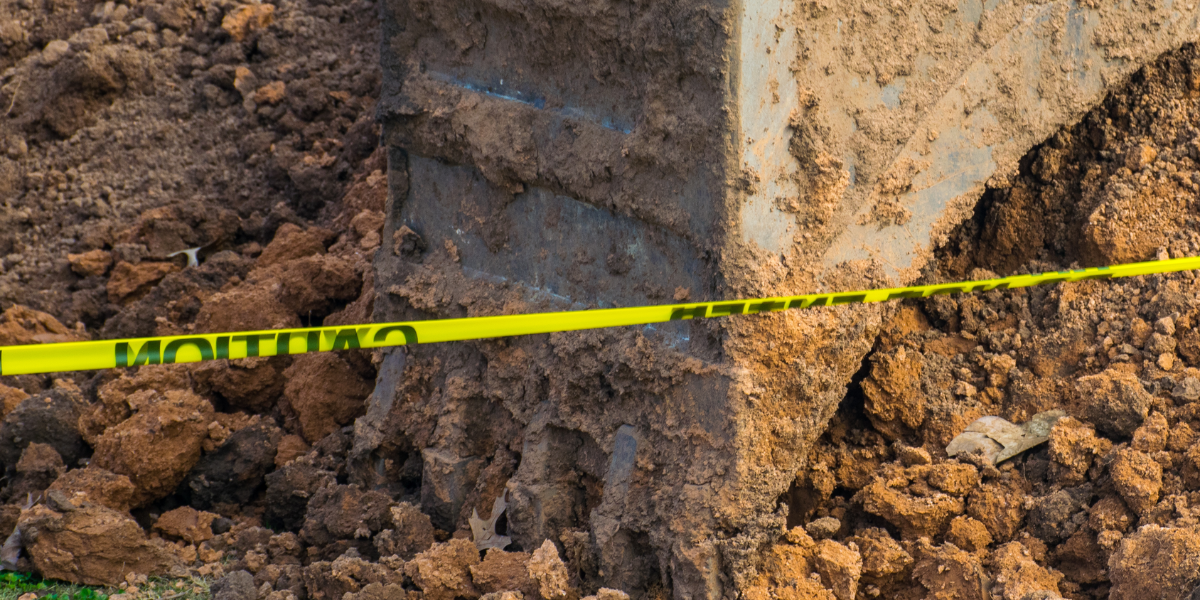
This article was published in the 2024 Excavation Safety Guide.
I am often asked how to better investigate a damage in order to beat paying for it. While I get the point of the question, the real purpose behind the damage investigation is to get to the truth of what happened. If the excavator is wrong, no amount of manipulation is going to change this fact. A good investigation, however, can tell what went wrong and how to change or improve things to prevent damage in the future. If the excavator did everything right, but has little or no documentation, they again find themselves involved in a claim. Excavators continue to find themselves in claims disputes because, in general, they don’t do an adequate job of documenting a damage. To be fair, utilities don’t do a good job either which leads to disputes and, in many cases, litigation.
A quality investigation can defend an excavator against unfair claims and literally save thousands of dollars. With just a few key processes in place, excavators can set themselves up for success in the event of an unforeseen incident. One of the most overlooked tasks necessary for a quality investigation occurs long before the incident ever happens. Taking photographs or video after locates are complete and before excavation begins can be critical in telling the story of a utility damage. Once excavation begins, the site changes forever; marks are destroyed making it impossible to know what the area looked like before the damage without the aid of pictures. Many court cases have been lost because the contractor could not prove their claim that a line had not been marked or was mismarked prior to the damage.
It is necessary to capture an overview of the area that provides a geographic reference to place the photograph at the location. Date and time are important and many cameras have this information built into the metadata even though it may not show in the picture. Photographs should follow the path of the proposed excavation along with potential crossings of other utility lines. Even if there is no paint, pictures should be taken. If a line is struck, those photos will clearly show the absence of paint or flags. You can’t take too many pictures. Pictures cost nearly nothing with today’s technology, so take plenty.
Video can be an excellent addition to the documentation process. The concept is the same as with photography, except the videographer has the ability to narrate as the scene is captured. Talking about the marks (or lack of marks) as well as what will take place can be a powerful piece of evidence should things go wrong. Background noise and opinions should be kept out of the video. I’ve seen numerous videos produced that had great content, but the narration was filled with opinions and conclusions that were later proved wrong or with an obvious bias against the other party which hurt the contractor’s case. Stick to the facts.
Potholing activities should be documented with pictures and video when possible. In many cases, open excavation will destroy any sign of potholing and if an incident occurs there will be questions as to whether potholing took place. Unfortunately, if it isn’t documented, it might as well have not happened. This documentation will show the utility in question was safely exposed without damage, which can be helpful if something goes wrong several months or years down the road.
Once all utility responses have been verified and the potholing has been completed and documented, excavation can begin. It is a good idea to periodically take pictures and video throughout the excavation process.
All this documentation will certainly help to reduce damages, however, despite doing everything right incidents still happen. When they do, a quality investigation will get to the truth of what happened. Several steps are necessary to ensure a proper investigation.
First, do not leave the scene. If you are not on site, arrive as quickly as possible. It is necessary to preserve evidence and make sure that nothing occurs that may corrupt the scene. The first priority is to ensure the area is safe for workers and the general public.
Once it is safe to do so, pictures and, if possible, video should be taken of the scene. In the event of a natural gas release, always seek permission before using a camera as it could be an ignition source. Many efforts to document an incident result in four to eight pictures of a damage in a hole and not much more. While it is important to capture the actual point of damage, those pictures by themselves do little to help the case.
Damage investigators should remember they are telling the story of the damage through photos or video to someone who will likely never go to the site - an internal risk manager, insurance adjuster, utility claims representative or even a utility expert hired to review the case. Companies should develop a standardized process for photographing a scene that is easily repeatable.
One easy solution is called the “clock method”. Using the center of the clock as the point of damage, the investigator starts at 12 at a distance away from it; potentially 50 feet or more depending on the size of damage and scope of work. A picture is taken looking toward the damage. The investigator moves halfway toward the damage and takes another picture. Moving close to the damage, the investigator takes one more. This process is repeated at the clock position 1:30, 3:00, 4:30, 6:00, 7:30, 9:00 and 10:30. This generates 24 pictures from varying perspectives. Designed for use with a disposable camera where there was no opportunity to review the photos prior to developing them, even with today’s advanced digital cameras and cell phones, it is a good way to standardize the process of photography.
Additionally, photos following the path of the excavation and the path of the marks should be a point of emphasis. One key component of these pictures is a measuring device. Photos without these devices are fairly worthless when the dispute is whether marks put down were within the tolerance zone of the damaged utility line.
While a tape measure is fine, there are several products on the market which are very easy to see in photographs.
It is important to capture individuals involved in the incident in the pictures, including construction staff, locators, utility representatives and witnesses. If the case should go to litigation, this places them at the scene at the time of the incident. Vehicle photos including license plates may be helpful in determining the identity of an uncooperative representative. Video should follow the same basics process.
The next step of the investigation is to draw a diagram. This should be done on site during the investigation, not later at the office where details may be forgotten. This diagram should contain landmarks, directions, marks (if present), the path of excavation and all other important information. It doesn’t matter if the investigator is not an artist. The drawing can be cleaned up or reproduced in a software program later. Pictures can be added, and comments, directions, names and other details can be overlaid on top of the photos to tell the story of the damage.
It may be possible to utilize a Google Earth image and redraw the diagram on it. The purpose is to help tell the story of the damage. Photographic locations can be added to the diagram to help provide perspective.
Interviews can be another important part of the investigation, including the excavator’s staff, the locators and the utility representatives. In many cases, the locators and utility representatives may refuse to give a statement but an attempt should still be made. If litigation occurs, the investigator may find him/herself in a deposition in which the question is asked about whether he/she talked to the other sides. If the answer is no, it will be easy to spin the testimony to sound like the investigation was one-sided and didn’t consider other parties. If other parties refuse, it should be documented on the investigation report. With this, the answer becomes, “I tried, but they refused to talk to me”, which changes the dynamic and should diffuse that line of questioning. If they do talk, it should be documented and if possible, signed.
Along with interviewing internal staff, statements should be collected from those on site at the time of the incident. Each employee should write a personal statement about what they were doing when the damage happened and what was observed. The employee should sign and date this statement. Never write a group statement and have employees sign it. This can be made to imply the company is telling the employee what to say. After personal statements have been gathered, it is fine to gather everyone together to talk about what they saw as a group. One prominent attorney uses this technique to tap into what he calls their collective conscience. By getting them together, one employee may remember one thing that spurs the rest to build on the point and additional facts may be revealed.
It is important that, regardless of the investigation form used, it is completed entirely. “N/A” is better than a blank field. Blank spaces can lead to the perception of an incomplete report. Forms should be completed on site; waiting to get back to the office can lead to errors and loss of needed facts. One error could lead others to question the accuracy of the entire report.
Once all information has been collected, it is important to store it in a location where it can be easily retrieved at a later date. Because invoices for damages can come months or years after the incident, storage and retrieval are necessary requirements of any damage investigation process. This is one of the main reasons it is critical to thoroughly document a damage. After the incident, life goes on. Other jobs continue and the memory of the incident can fade away. Employees may leave, taking with them valuable information. A thorough damage investigation helps remind everyone of what actually happened and fills in the gaps caused by memory loss and employee turnover.
Simply put, a quality damage investigation puts your company in the driver’s seat.
Ron Peterson is dedicated to damage prevention and improving safety within the industry. In addition to providing damage prevention and investigation services as owner of Ron Peterson Consulting, Ron has held the position of Executive Director of Nulca since 2009. Ron can be reached at ron@ronpetersonconsulting.com.