GPR is a non-invasive technology that uses an antenna to send electromagnetic pulses into the ground and records two-way travel times of waves and amplitudes of reflections. When the wave moves from one set of physical properties to another, some of the energy is reflected towards the ground surface. The two-way travel time can be converted into depth if the user estimates the velocity that the GPR wave traveled. If the contrast between the two materials is large (a metal pipe buried in sand), then most or all the energy will be reflected. If the contrast between the two materials is small (the contrast between concrete and sand), then some of the energy will be reflected and some will continue into the next material. This allows for the possibility of additional reflection events at greater depths and this is what makes GPR a truly three dimensional imaging technology. If enough scans are collected, and the locations of those scans are known relative to each other, then the data can be resampled into various 3D visualizations such as time-slices/amplitude maps, volumetric cubes, fence diagrams, and iso-surfaces. The ability to visualize these data in many forms can assist the engineer in solving problems using GPR technology.
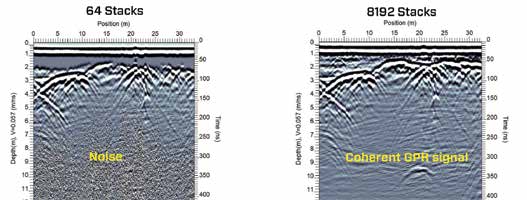
Despite its dynamism, GPR is not a tool that can be used in isolation of other non-destructive technologies. There are advantages and disadvantages to GPR and the principles of other techniques often complement GPR.
Advantages of GPR
• easy to use
• easy to set up
• can be used with various frequencies which can be applied to unique applications.
• works on contrast and thus has the potential to identify targets of interest or evaluate infrastructure aboveground or belowground, no matter what the material is.
Disadvantages of GPR
• general inability to determine exactly what material caused a reflection based on the GPR data alone.
• electromagnetic signal is susceptible to rapid decay when traveling through all materials except air which limits depths of investigation
• GPR receiver will record all electromagnetic (EM) signals propagating towards it including those that were not generated by the GPR itself. These external sources of noise can cause static in the GPR data, decrease quality and clarity, and ultimately make it difficult to interpret.
Ways GPR can be used in damage prevention
1. Locating buried pipes and utilities
GPR is a great complement to traditional EM locators because it can be used to locate any material underground so long as there is a contrast between the target and the soil in which it is buried. GPR can locate wire and cable, but also pipes made of PVC, clay, fiberglass, or other materials that do not hold a current. The outputs of GPR scanning can be used during the design phase to increase effectiveness or during construction to avoid damages. GPR is often used in conjunction with EM pipe/cable locators to maximize the likelihood of identifying all underground services that are identifiable.
2.Concrete scanning
GPR with high frequency antenna can be used to determine concrete thickness and to locate, map, and mark post tension cables, steel rebar, wire mesh, or other reinforcements embedded in concrete structures. This is important for maintaining structural integrity during concrete cutting, drilling, or coring and will minimize the probability of unnecessary costs due to damage. In addition, identifying locations of potential live conduit can increase site safety and minimize the likelihood of injury while drilling into concrete. One difficulty GPR can have with concrete is identifying internal defects such as honeycombing or delamination. While this is possible since the air inside the defect will contrast with the concrete, it can present trouble for GPR since the size of the defect might be too small for GPR to record a response. GPR is often used in conjunction with ultrasonic pulse echo, which works on mechanical waves, to identify minor defects that can be catastrophic to structural integrity if not mitigated.
3. Evaluating conditions of roadways
GPR can provide early detection of voids that may be developing below a paved surface and cracks or emerging cracks in actual roads that might not be visible from the surface. Unlike coring, GPR offers a non-destructive way to assess roads for current deterioration levels, remediation planning, and ultimately extend the use life of this critical asset. Road condition assessment is an application that often requires a range of GPR frequencies to fully identify potential sources of road failure, lower frequencies for deep void detection and higher frequencies for asphalt and base condition assessment. New GPR technologies are now available that provide the engineer with the ability to collect information at highway speeds which can increase project safety, minimize disruption to the flow of traffic, and potentially provide rapid dissemination of deliverables to clients. In addition to GPR, falling weight deflectometers can assess the strength of roads and provide additional information beyond what GPR can reliably produce.
4. Locating buried contamination
Before grading and excavation for foundations, GPR can be used to pinpoint the locations of debris for removal. GPR can determine density, depth, and amount of debris on a site. Large amounts of buried debris may make sites unsuitable for construction and GPR can be used for rapid assessment to inform decisions. Also, GPR can be used to evaluate soil contamination on construction projects or brownfield sites in general. The GPR signal can rapidly deteriorate when traveling through certain contaminants and the engineer may attempt to identify locations or boundaries of signal decay to assist in interpretations of contaminant plumes. A complementary tool for identifying debris and soil contamination is a conductivity meter which records the ease or difficulty of inducing an electric current in the subsurface. For example, concrete debris buried in clay would be less conductive and thus more difficult to induce a current into compared to the clay around it.
5. Evaluating corrosion of rebar
Corrosion of steel rebar in reinforced concrete creates long-term durability problems during the service life of a structure. The process of corrosion alters the chemical properties that results in the loss of area in the reinforcing steel. These alterations allow GPR to distinguish between corroded steel and unaffected rebar, allowing engineers to adequately evaluate structural quality and integrity. Another useful method for evaluating corrosion of rebar is a half-cell potential sensor. This technique applies an electric current to a healthy steel rebar embedded in concrete and measures the impact of that signal across the structure.
Whether you own a GPR unit, rent equipment, or hire an outside expert, this technology can cut project costs, limit liability, increase site safety, enhance the design phase, and grow your business. Many firms do not use GPR or only use it on a limited set of projects. By integrating this technology into your proposals and projects, you can win more work and add additional service offerings to your clients.
is President of Bigman Geophysical (bigmangeo.com), a company providing training, equipment rentals, and project support for the damage prevention industry. He is instrumental in the development of the GPR Congress, a forum for academic and industry practitioners to engage in open discussion and continuous learning through shared ideas and experience. Learn more at GPRcongress.com.
Comments